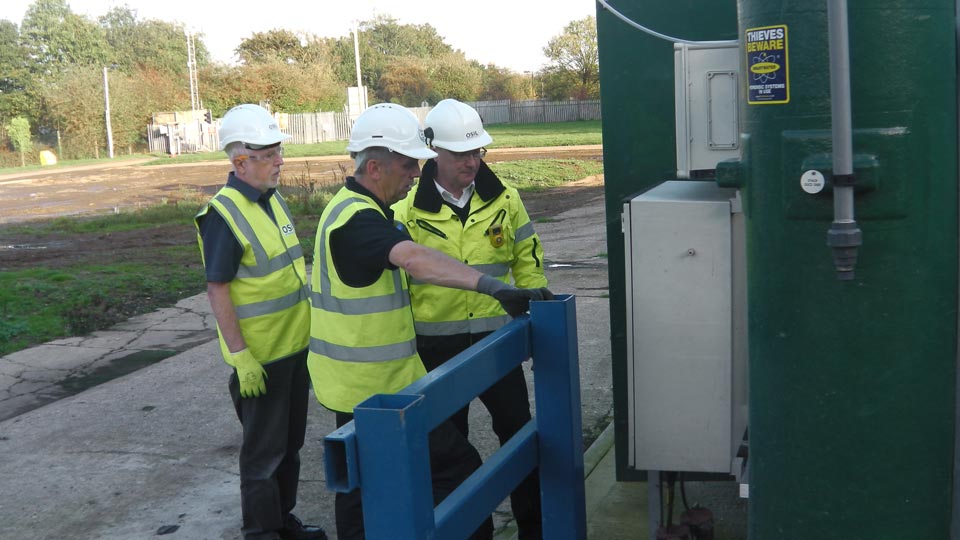
Service and maintenance is all about making sure things work properly, but there’s a lot more to it than simply scheduling appointments.
Companies that are serious about their air pollution, ventilation and odour control systems need an optimised service and maintenance strategy.
What is a service and maintenance strategy? It’s a strategy that defines your system’s operational requirements and how these requirements can be met with service and maintenance. It is not a static strategy, but an adaptive strategy that changes when you identify improvements and new requirements.
Some companies will buy engineered equipment, put routine service and maintenance dates into their calendar and forget about it. This is a missed opportunity to optimise service and maintenance to achieve real business benefits.
Structure and schedule
Optimised service and maintenance strategies do away with “tick and flick” style routine maintenance. The risk of “tick and flick” maintenance is not identifying future problems and inspecting hardware at only a minimum level.
Rather than promote bare minimum maintenance, more intensive checks can be deployed to catch problems and reduce the need for future, costlier repairs. Consider structuring your maintenance strategy to work at a higher level.
You’ll be able to plan better
By structuring and scheduling your service and maintenance, you’ll be able to plan uptime and downtime perfectly. This is beneficial for your business and customers. You can reduce unplanned maintenance by 90% with a good strategy.
Operational focus
Some companies are reluctant to take equipment out of service for maintenance. This can end in disaster. What is the point of putting off service and maintenance for a week, if doing so could put the equipment out of action for two weeks?
Without maintenance, you risk even longer downtime and more expensive repairs when something fails. Optimising your service and maintenance strategy to recognise this so your operation is focused on uptime will be a smart decision.
You’ll manage costs better
An optimised service and maintenance strategy will allocate your budget to the right places. You will significantly reduce unplanned maintenance. The cost to maintain equipment will be less because maintenance will be a properly planned routine, not reactive.
Missed opportunities to improve
The “leave it and forget it” approach to air pollution, ventilation and odour control systems only works when you ignore the fact that technology moves on. These systems get more efficient and better at their jobs with each generation.
An optimised service and maintenance strategy recognises these advancements in technology and deploys them whenever suitable. Engineers should look for opportunities to make systems more energy-efficient and cleaner.
You’ll build knowledge in your systems
Experts have a way of keeping knowledge in their heads, and when they leave, that knowledge goes with them. With an optimised strategy, your engineers will play a lead role in developing maintenance guidelines and best practices for your systems.
Avoid reactive routines that overcompensate
Sometimes, hardware failures cause panic, leading to reactive work that tries to solve problems that don’t exist. The problem here is spending money on unnecessary work and engineers wasting their time doing pointless work.
With an optimised service and maintenance strategy, you will take a deeper look at your systems, hardware, and monitoring practices. You will specify the hardware that is a cause for concern and ensure all non-issues remain non-issues.
Want to find out more about service and maintenance strategy?
Call us today on +44 (0) 1543 506855 to speak with one of our experts.